If you're a cannabis producer, streamlining operations and continually identifying ways to improve your processes is essential to staying competitive in this industry.
A great example is Tantalus Labs, a cannabis producer based out of British Columbia. Its CEO, Dan Sutton, recently took to Twitter to share the company's progress over time and how continuous improvement has led to profitability.
CRAFT CANNABIS LIFE PRO TIP: collect data on every process that influences the consumer's perception of the quality of your products.
— dansutton.eth (@DSutton1986) July 8, 2022
Nutrients, light, harvest times, drying, curing, trimming, packaging, QA all important targets. Tools like @ElevatedSignals can help with this. pic.twitter.com/c1aoXfUOMh
We’re all about helping cannabis businesses achieve these results, so we called our friend Tom Smale over at Growbox Consulting to discuss the common operational mistakes he sees in cannabis cultivation facilities and how to fix them.
Tom's specialty is working with cannabis growers across Canada to help them perfect their grow and produce high-quality flower. His methodology is embedding himself into the client's operations to identify areas of improvement, leading to streamlined processes and better quality products.
In this post, Tom covers the top operational mistakes he sees cannabis producers make and shares best practices for overcoming them.
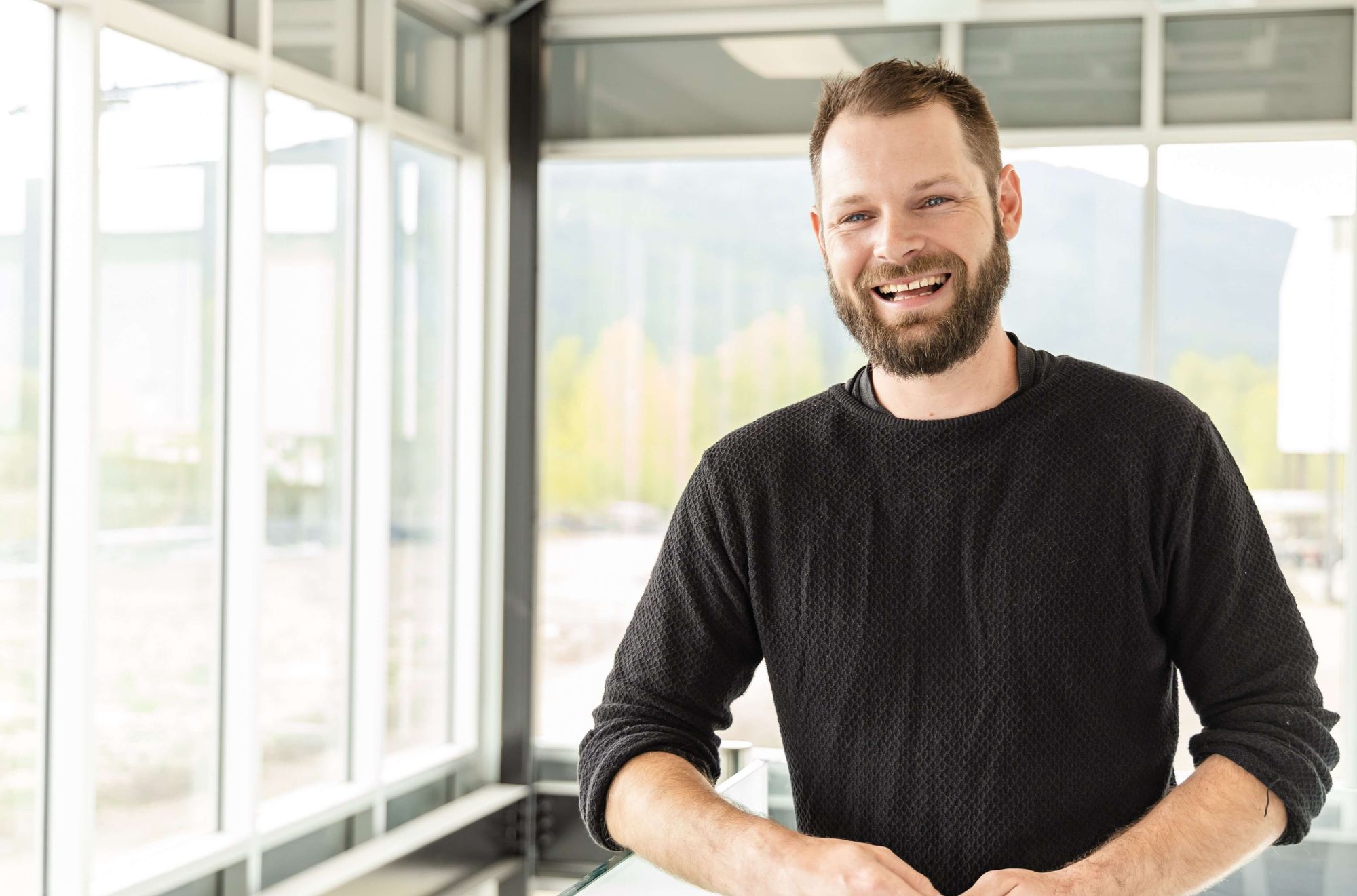
Operational Mistake #1: Overcomplicating operational documents
According to Tom, one of the most common operational mistakes cannabis producers make is overcomplicating their procedures - specifically SOPs and documentation.
Although the cannabis industry in Canada is highly regulated, it doesn't necessarily mean your procedures need to be complex. "We see this problem a lot since many quality principles are relics from the pharmaceutical and food industries," Tom says.
“Overcomplicated SOPs don’t have the flexibility for cannabis cultivation, leading to deviations from the procedures and additional QA work,” he adds. SOPs should be easy for staff to understand and accurately reflect cultivation procedures.
Tom says he often sees SOPs that don't allow cultivation teams to achieve their harvest goals. Meanwhile, when growers deviate from SOPs, it means dealing with deviations and investigations for QA.
Having Operations and QA teams misaligned on procedures can cause batch release delays due to additional quality documentation. Not only is this inefficient, but it can also lead to purchase order fulfilment delays and lost revenue.
Producers can avoid these situations by creating mutual understanding between QA and Operations teams.
"QA staff should take time to learn cultivation methods and how they help growers reach harvest goals. On the other hand, master growers and cultivation staff also need to learn the expectations from the QA department," recommends Tom.
"Cultivation procedures need to be balanced and give the cultivation team some flexibility while staying compliant with the regulations," Tom adds.
If you don't know where to start, consider these two key areas:
- Invite quality teams to learn about the cultivation process and train cultivation teams on relevant regulations that apply to their job duties.
- Audit your processes and look for areas that are causing deviations. These might be procedures that you can update in SOPs.
Read: “Why are SOPs important for a successful cannabis business?”
Operational Mistake #2: Putting product quality on the backburner
There's a not-so-secret pathway to increased revenue for cannabis production - it's producing quality flower!
Making quality products may seem like a no-brainer, but it's an issue Tom often comes across. "In cannabis, we often see companies cutting costs, chasing purchase orders and racing to market without prioritizing product quality," he explains. It's often an overlooked operational mistake that leaves revenue on the table.
In one case, Tom said the air conditioning broke in a grow room, and the company wasn't prioritizing repairing it. This directly impacted the quality of the product grown.
"You only have a small window of opportunity to make a good impression on your customers. You need to invest in the growing process and focus on producing quality flower."
On several occasions, Tom has seen grows in such bad shape that he has had to restart the growing program completely. They then start to see healthy plants, and naturally, more purchase orders start coming in because customers are happy with the product.
Tom believes cannabis companies should invest more resources into cultivation to grow better flower; he recommends:
- Build a growing program around guard rails, with Integrated Pest Management (IPM) and sanitation being fundamental pillars. Make sure your procedures are built around the growing process and allow Master Growers to do their thing!
Read: “Common cannabis cultivation challenges and how to improve them”
Operational Mistake #3: Transparency; don’t lie to Health Canada and Canada Revenue Agency
"We see this all the time, Health Canada coming for an audit and the team stalling the inspection and falsifying documents to make them look compliant," Tom explains. "This strategy never works! Inspectors are experienced and always find the things you're hiding."
Tom told us about a facility that provided falsified documents in response to a question from an inspector during an audit. This deception led to two more unannounced inspections and critical observations. "This wouldn't have happened if they were truthful. They broke trust with Health Canada," he said.
Tom advises all of his clients to be transparent to avoid this operational mistake. He also teaches them how to address observations and present information to make their audits easier.
"I recently assisted a client with a sales-amendment inspection. We had proper documentation and were super organized, and because of that, we received the amendment in seven days.”
Here are Tom's tips on best practices to prepare for audits:
- During inspections, own up to missing procedures, deviations, and complaints. These are ultimately all common things that happen in a facility. Being honest and upfront will lead to fewer major or critical observations from Health Canada.
- Ensure your team understands how to respond to observations addressing Health Canada concerns. If you don't know where to start, consider finding a consultant to help you.
Read: “What does Health Canada ask during a cannabis regulations inspection?”
Operational efficiency is key to the success of cannabis businesses
Being a cannabis producer is expensive, and the market is increasingly competitive. Tuning operations can be the difference between a struggling business and a successful one.
Building efficiencies in your procedures, focusing on the quality of your product and improving your relationship with the regulators can help your team save heaps of time and unlock revenue.
If you’re interested in learning more about how your cannabis company can reduce operating costs - check out our cannabis software buyer’s guide!