A Success Story 🚀
Heritage Cannabis is a leading cannabis processor with multiple facilities across Canada with complex workflows across extraction, packaging, and fulfillment. Not long ago, its operations were bogged down by manual batch records, constant document errors, and hours of wasted QA time.
The switch to electronic batch records (EBRs) with Elevated Signals started as a fix for human error, but quickly became much more, laying the foundations for data-driven decision-making and operational efficiency.
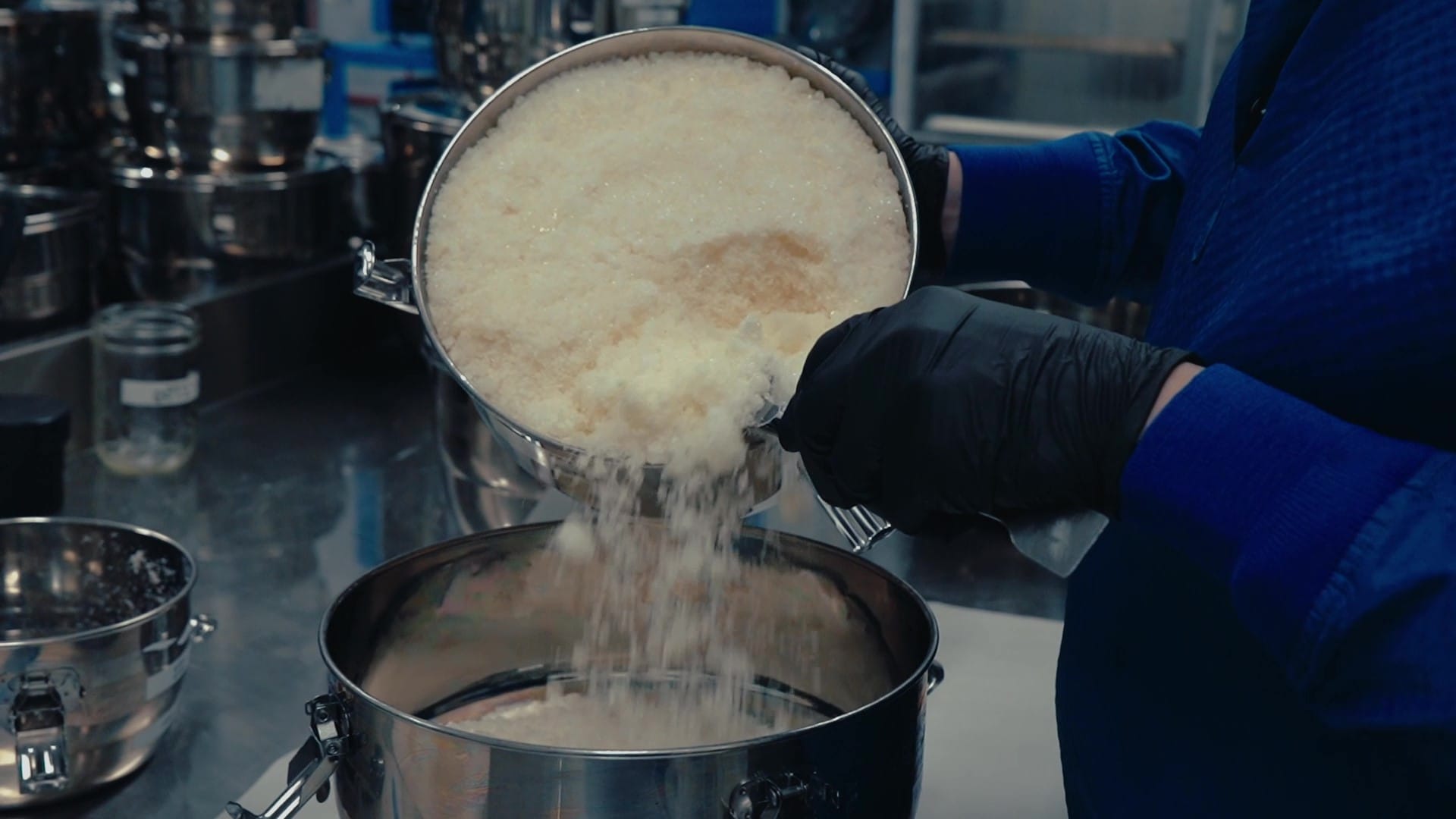
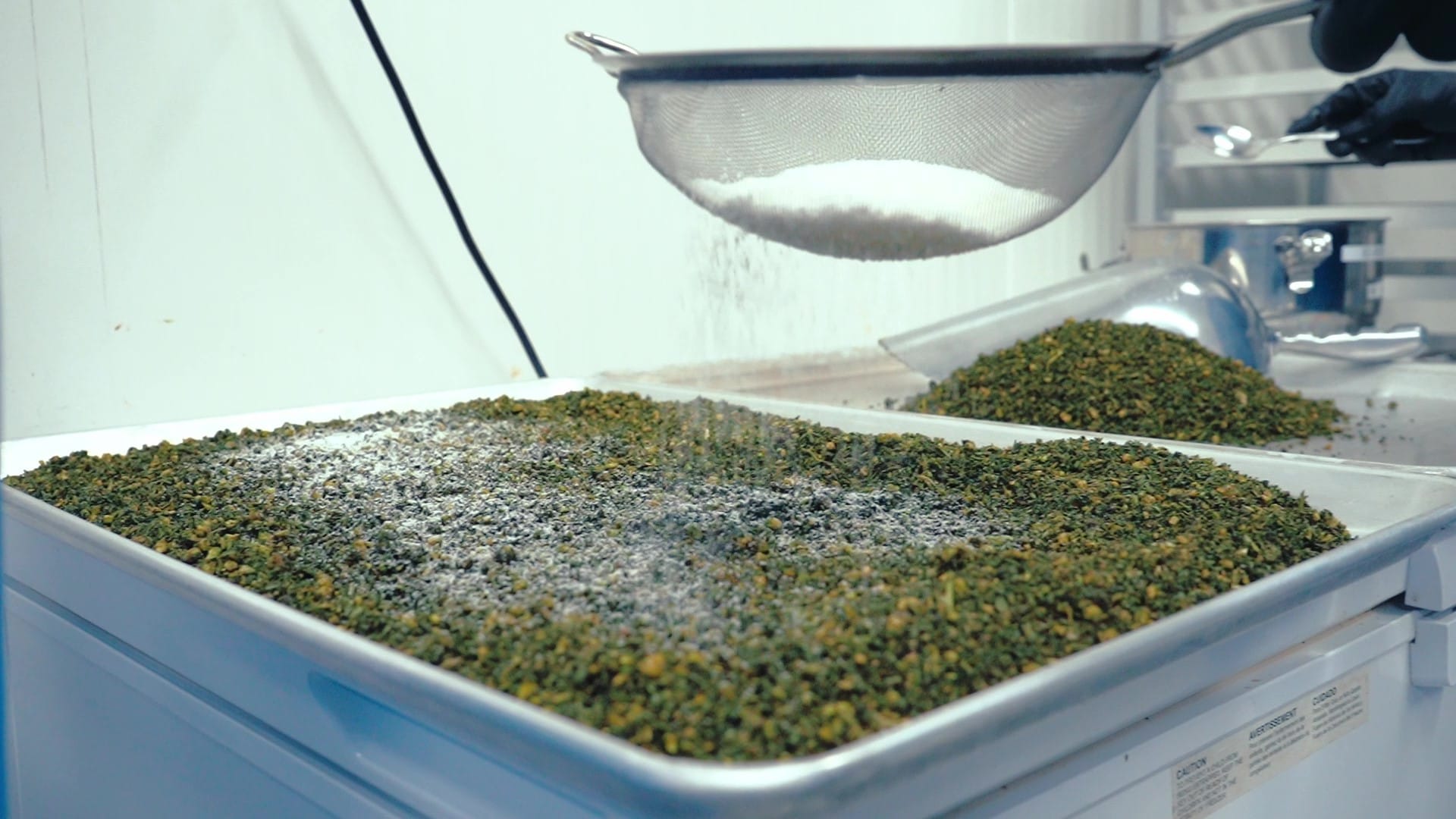
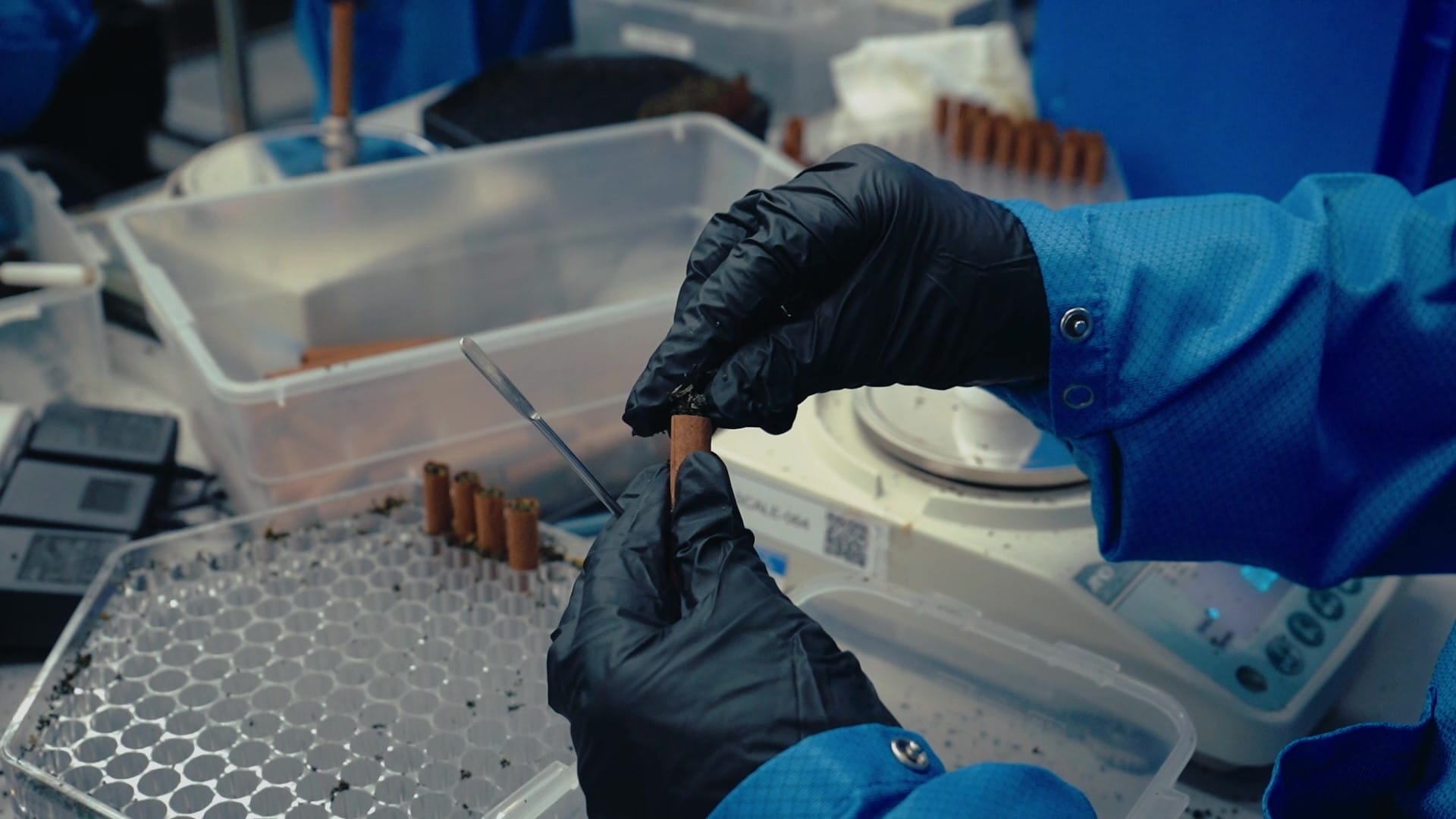
Credit: Heritage Cannabis
The QA overhaul that ended paper problems
Before EBRs, paper ruled the floor.
- QA had to return the same record to production three or four times due to gaps or incorrect information
- Misplaced, hard to track down the hard copy, creating compliance risks
- QA wasted time physically walking papers across departments, slowing batch turnaround
- Filing paper took hours every week, leaving little time for higher-value work
“I was reviewing paperwork all day. I once made a 50-slide training deck just to get people to fill in forms properly. Nothing stuck.”— Kat Andersen, QA Associate, Heritage Cannabis
Since adopting Elevated Signals’ electronic batch records, the process has changed completely:
- Required fields ensure no data is missing
- Auto-calculations eliminate math errors
- Status-based workflows prompt each team, so they know what the next step is
- Remote access lets the Heritage team review and return records instantly, even off-site
“I don’t have to chase anyone down anymore. I change the status and they’re notified. It’s that fast.” — Kat Andersen, QA Associate, Heritage Cannabis
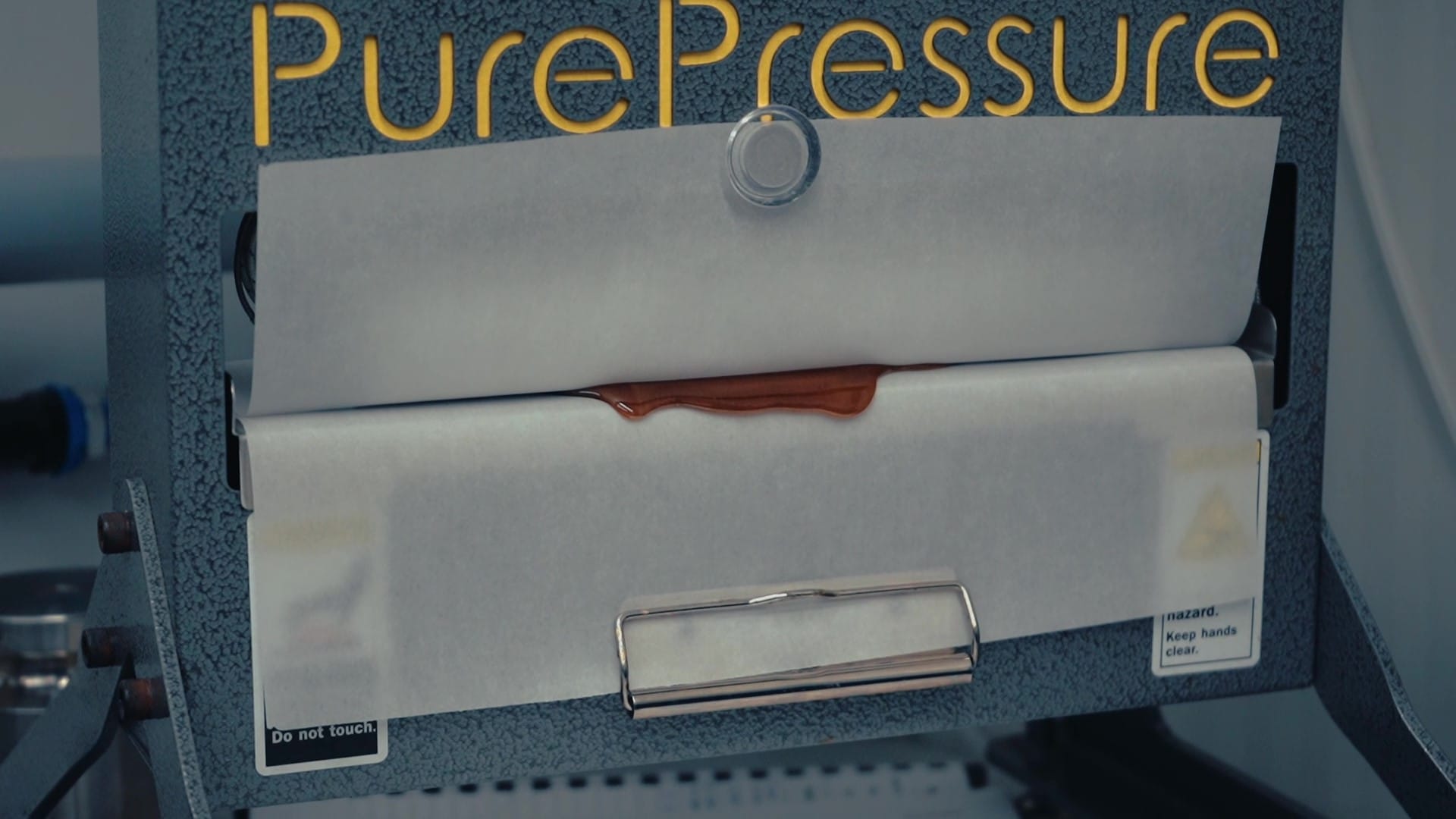
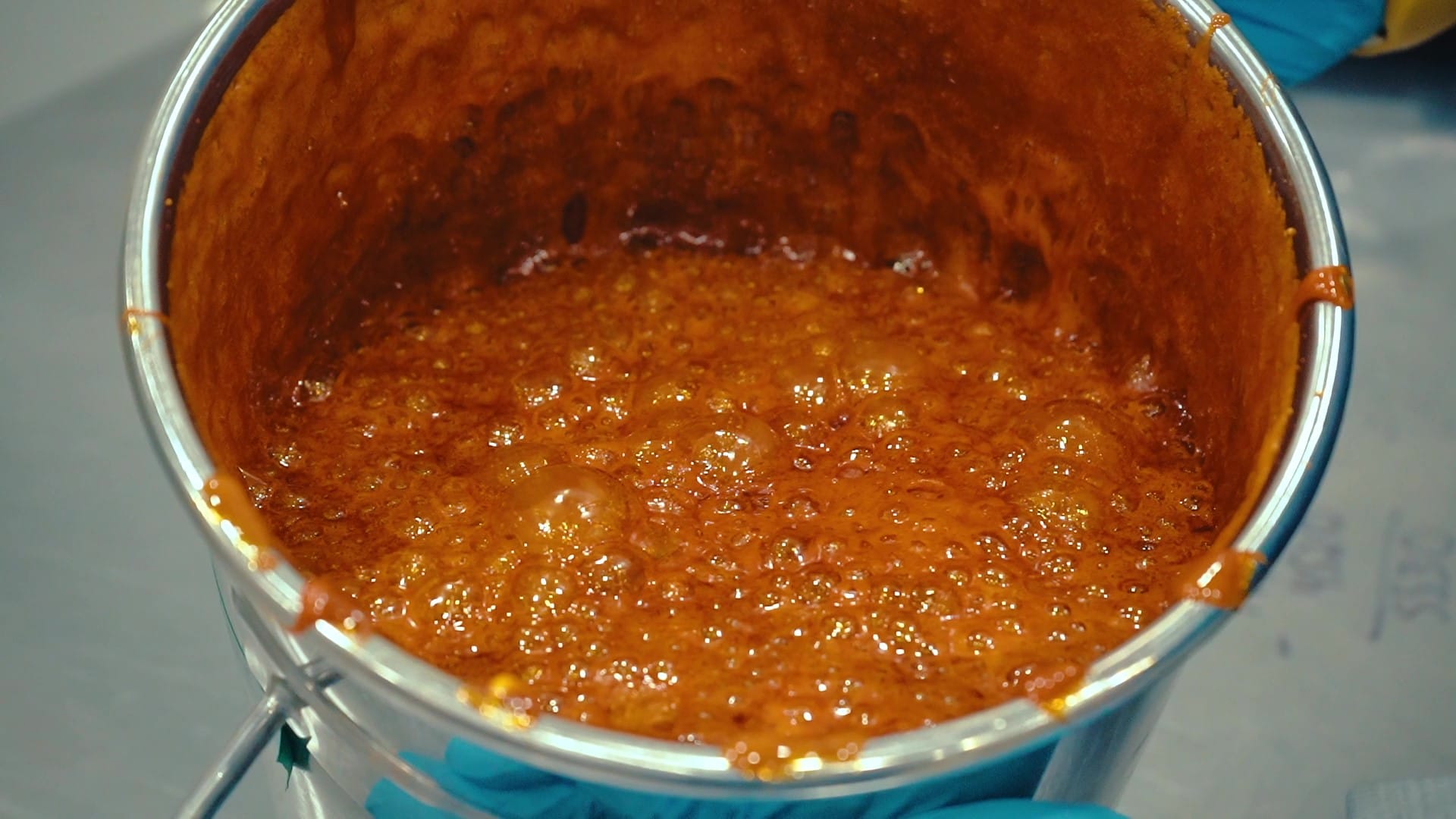
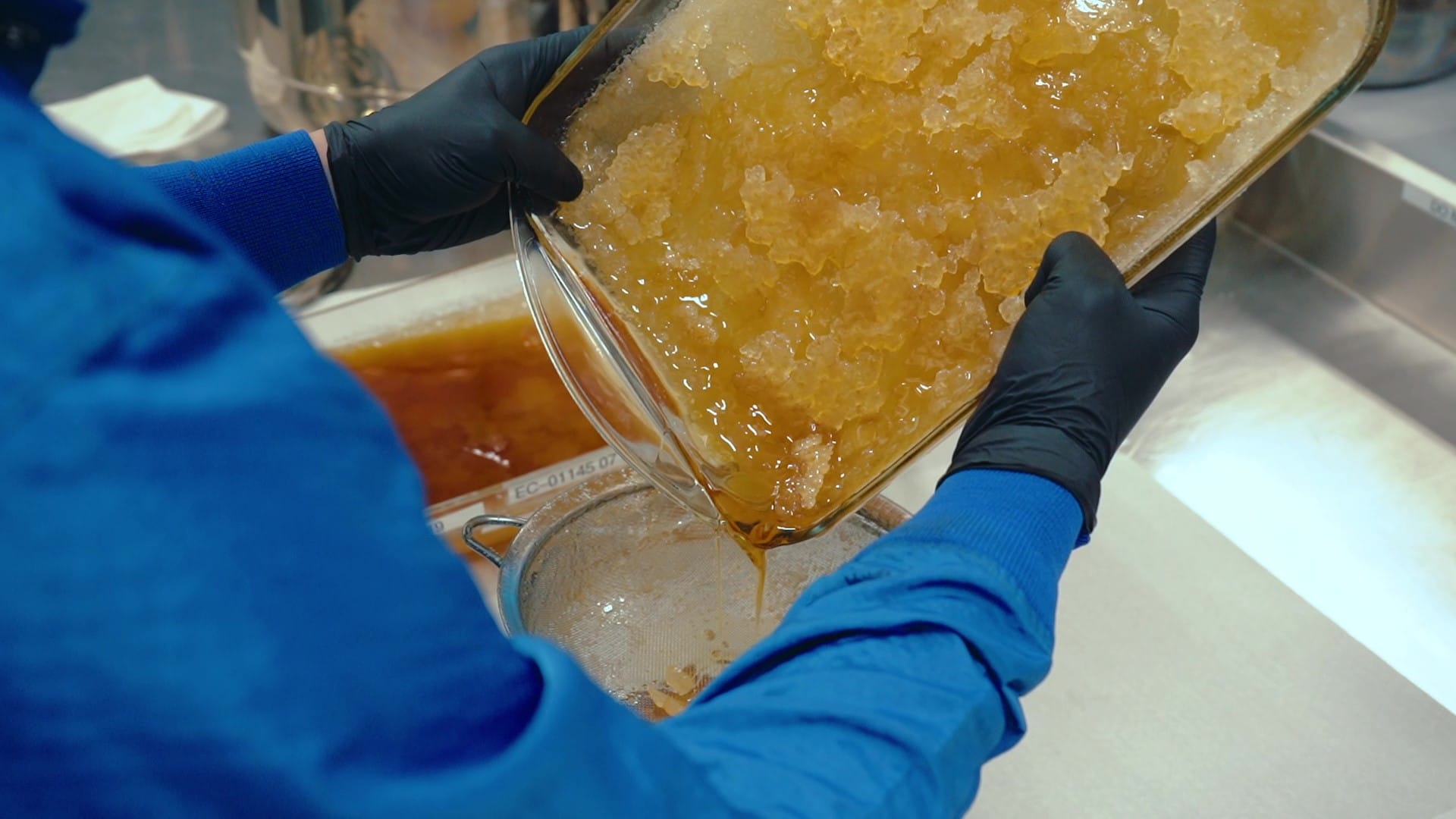
Credit: Heritage Cannabis
How Heritage turned raw batch data into actionable insights
EBRs didn’t just reduce paperwork, they unlocked the possibility of powerful insights from production data that was previously trapped on paper.
Heritage now uses custom dashboards to monitor production efficiency, track right-first-time metrics, and analyze time-per-unit across SKUs. Managers now get real-time visibility into bottlenecks and trends, without chasing down spreadsheets or reports.
“Now we’re tracking KPIs and building dashboards that shape how we run the company. It’s gone way beyond what I expected.”— Kat Andersen, QA Associate, Heritage Cannabis
This shift has laid the groundwork for smarter decisions and long-term profitability, helping Heritage move from reactive problem-solving to proactive optimization.
The Impact 🌱
âś… 50% Reduction in QA Admin Time
Freed up hours every week to focus on system improvements, not chasing paper or fixing errors.
âś… Right-First-Time Improved from 51% to 80% +
Built-in checks and required fields helped QA catch issues earlier, reducing rework and accelerating batch release.
âś… 90% Drop in Filing Time
Manual filing went from hours to minutes, simplifying audits and boosting compliance readiness.
âś… Custom Dashboards Driving Operational Insight
Heritage now surfaces trends, tracks efficiency by product type, and identifies bottlenecks using live data, not spreadsheets.

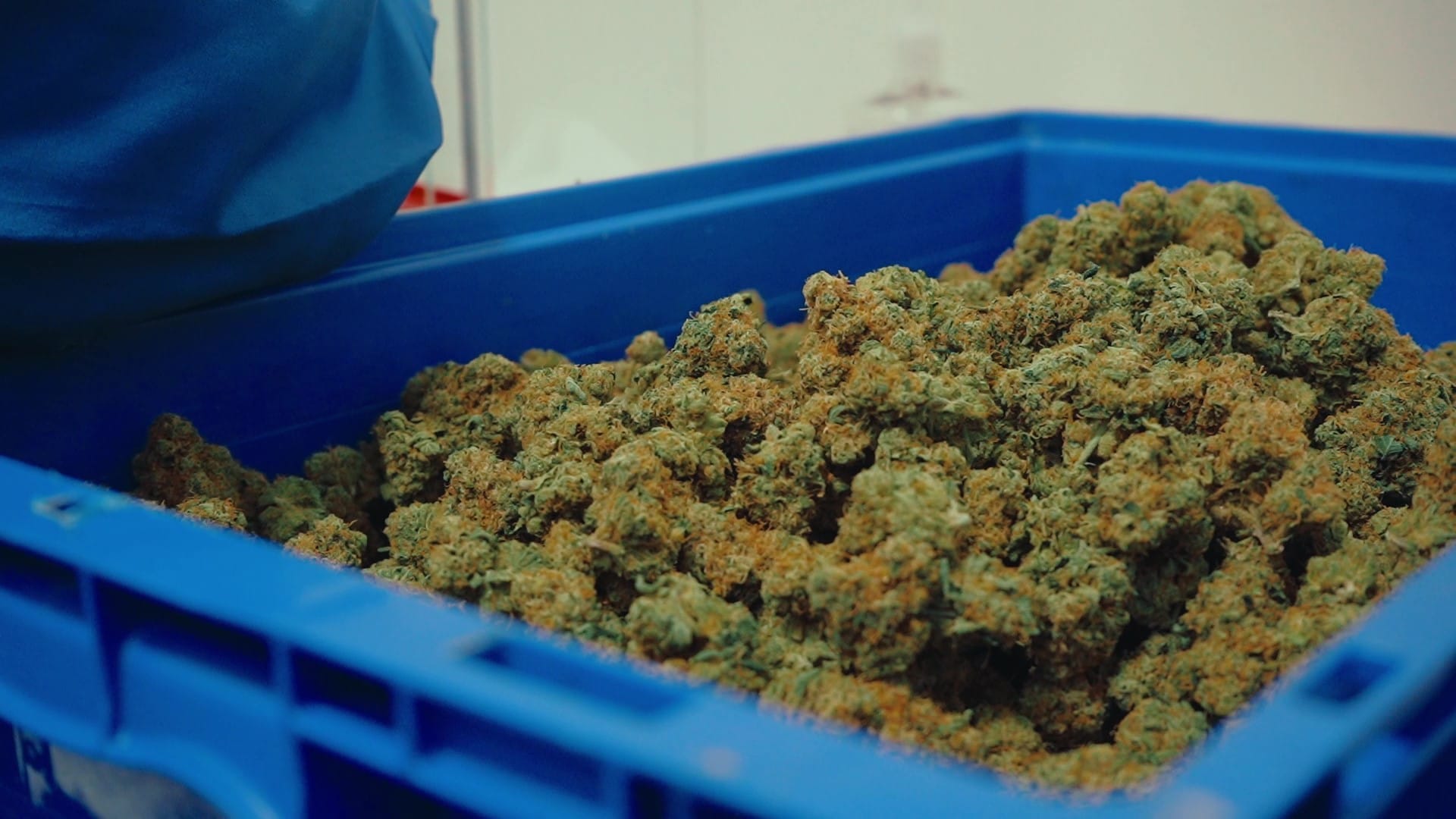
Credit: Heritage Cannabis